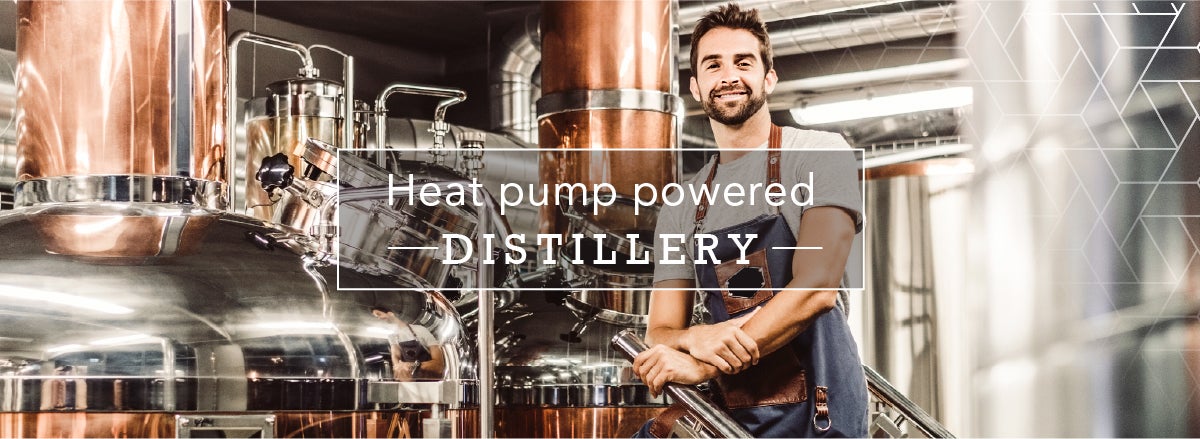
9/30/2021
Heat Pumps Help Create Energy Efficient Distillery
It's not easy to turn an industry that has traditionally relied on large amounts of energy into a low-carbon business. To brew up the magic, all top distilleries worldwide need to bring in heat. So how can distilleries reduce their carbon footprint while supplying enough energy to keep the processes running? One solution is energy-efficient heat pumps.
Technology in the form of ground and air-source heat pumps, which rely on natural heat, is gradually displacing fossil fuels for heating or cooling homes and buildings across the world. It only makes sense that distilleries, which rely heavily on a heat source for production, would explore the use of heat pumps.
A handful of both large-scale and small-batch distillers are turning to cleaner energy sources and high-tech operations to improve efficiency and product.
Connie Baker, Chief Distiller of Marble Distilling Co. in Carbondale, Colo. launched her business by pioneering a system that uses the distillery’s process water to heat the entire building, saving 4 million gallons of water and 75 metric tons of carbon per year. Marble Distillery’s water-source heat pump leverages the hot and cold tanks. By plugging into these tanks like thermal batteries, the heat pump can be used year-round, to preheat the mash tanks or to cool down the rooms of the inn. Within two weeks of making the switch to the electric heat pump, Connie Baker doubled her production and cut her utility usage in half.
Our neighbors up north, Pemberton Distillery, located outside ski area Whistler Blackcomb, in British Columbia, incorporated heat pumps into their business in 2008. Pemberton uses a geothermal system for space heating and a cooling mode that uses the excess heat for hot water heating. When in heating mode the system is 40% more efficient than a traditional system and when in cooling mode it is up to 70% more efficient as the waste heat from cooling the building instead of being released is captured and heats water for their copper pot stills.
Across the pond in Donegal, Ireland, Crolly Distillery uses two high-temperature heat pumps in their production. Rejected heat is being used to heat process water up to 85 degrees. The water is used at the start of the process of whiskey distilling, while excess heat is being used to heat the visitor center and distillery offices. Not to be outdone, Jameson Whiskey took heat pump technology one step farther in their latest expansion in 2018. With the rapid increase in heat pump technology, Jameson installed the first commercial Mechanical Vapor Recompression heat pump that recovers energy and reintroduces it into the distillation column further reducing the energy needed in distillation!
Within the brewing and distillation process, equipment providers continue to innovate and develop heat pump solutions to fit within the various beverage-making steps. One recent advancement is commercial heat pump equipment that can reach air temperatures of 248 degrees Fahrenheit that can be used for drying needs.
Heat pumps are a cleaner, efficient energy option
Until recently, natural gas was the most cost-effective energy source with the lowest carbon footprint among the fossil fuels accessible. A handful of distilleries have already looked into or implemented heat recovery systems to transition to cleaner energy operations.
Heat pumps have been around since the 19th century when they were first patented by American inventor Oliver Evans for use on his steam engine-powered flour milling plant in Philadelphia, Pennsylvania in 1804. They are currently one of the most widely used methods of transferring heat between two locations without using any other form of energy input than electricity to power them.
Heat pumps are similar to air conditioners, with the exception that they can function for both heating and cooling. Instead of only transferring heat from a space to cool it off, they can also bring in heat from another source to warm it up. This means that you can use electricity to provide hot air or water when you need it without having to burn gas or oil.
Installing heat recovery equipment in any distillery demands extensive process expertise due to the intricacy and sensitivity of the distilling process. Because gas is a very low-cost fuel, it is difficult for a distillery to decarbonize its processes while keeping the cost of production low. The distillery's issue is how to achieve a cleaner fuel source without incurring a significant increase in fuel costs.
Hydrogen energy is an option; however, it is three times more expensive than natural gas. As a result, distillers must develop a cost-effective solution, and electric heat pump solutions are an excellent place to start.
One of the many benefits of using heat pumps in the distillation process is that it reduces the quantity of waste heat released into the atmosphere. Heat pumps can save a distillery approximately two-thirds of the heat energy used in the still house.
Heat pumps are now the most cost-effective form of heating that uses electricity, with average COP (Coefficient of Performance) ratings of 2.5 or more, implying that they consume less than one kilowatt of electricity to create 2.5 kilowatts of heating or cooling power.
To put this in perspective, a traditional heating system with a COP of less than one uses more than one kilowatt of power to produce one kilowatt of heat power. This makes a heat pump system cost-effective to operate while also reducing your carbon impact. In large-scale production such as distilleries, these numbers can really be beneficial.
Beneficial Electrification is not Just About Reducing Energy Use
Beneficial Electrification provides greater opportunities to help co-op members meet their sustainability goals. One such co-op, Inter-County Energy Cooperative Corp., and its generation and transmission co-op, East Kentucky Power Cooperative (EKPC) is helping a distillery in Kentucky meet its environmental goals. Diago, a Lebanon, Ky.-based bourbon distillery had a company goal to power its distillery with 100% renewable energy.
Diageo representatives had already settled on building their distillery in Kentucky co-op country when Inter-County Energy CEO Jerry Carter suggested ways for the company to meet its commitment to renewables, including switching from natural gas boilers to electric boilers powered by renewable energy.
The $130 million distillery will operate on 100 percent renewable electricity, helping to make this one of the largest carbon-neutral distilleries in North America.
Perry Jones, President, North America Supply for Diageo stated, “This groundbreaking undertaking to electrify our operations and then power them with renewable electricity will result in one of the largest carbon-neutral distilleries in North America.”
Together, we can create a win-win situation for distillers that will provide the benefits they desire in terms of carbon reduction, energy efficiency and cost-effective production.
Electrify and Save™
--
About Tri-State
Tri-State is a power supply cooperative, operating on a not-for-profit basis, serving electric distribution cooperatives and public power district member-owners in four states. Together with our members, we deliver reliable, affordable and responsible power to more than a million electricity consumers across nearly 200,000 square miles of the West. Visit www.tristate.coop.
Blog Posts
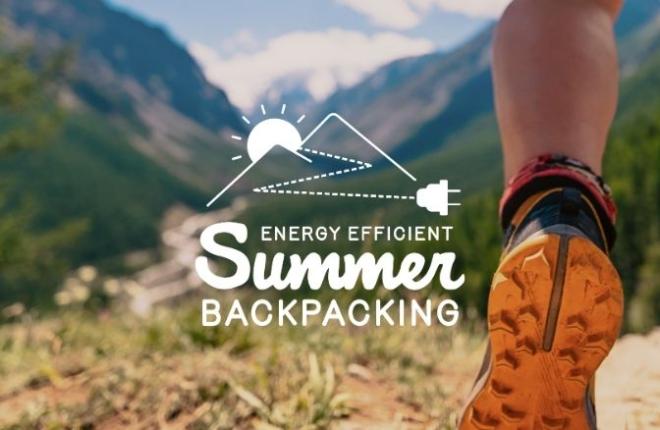
Summer Backpacking: Solar Power, Energy Efficiency, and the Best States to Visit
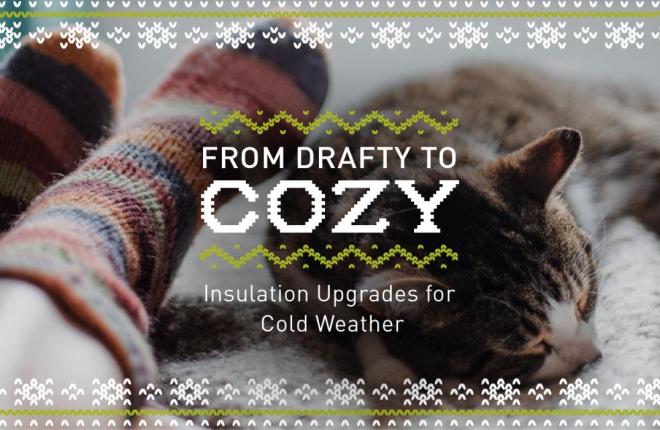
Beat the Chill: Effective Insulation Strategies for Winter Comfort
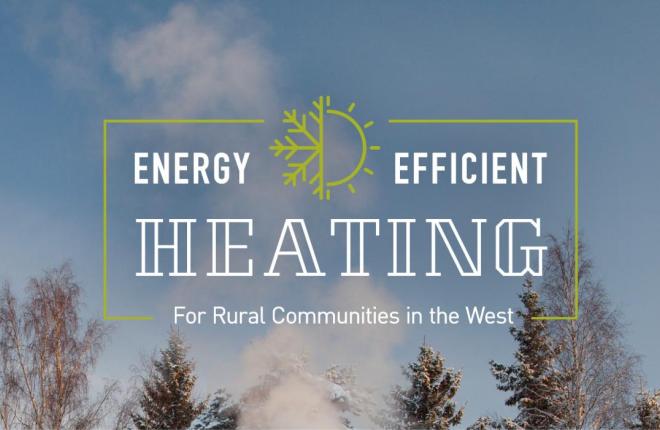
Energy Efficient Heating Options for Rural Communities in the West
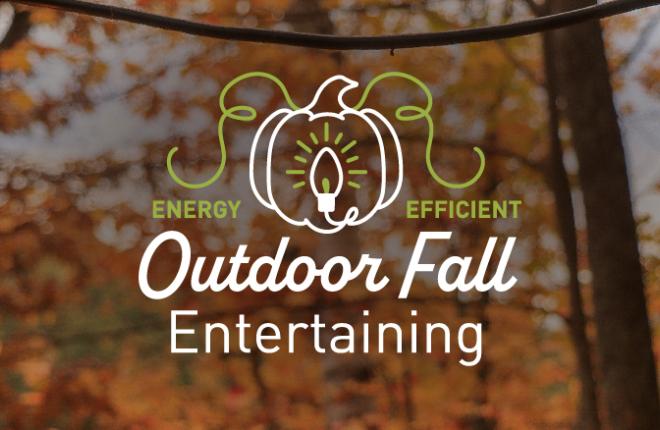
Energy Efficient Tips for Outdoor Fall Entertaining

Boost Your Business with EV Charging
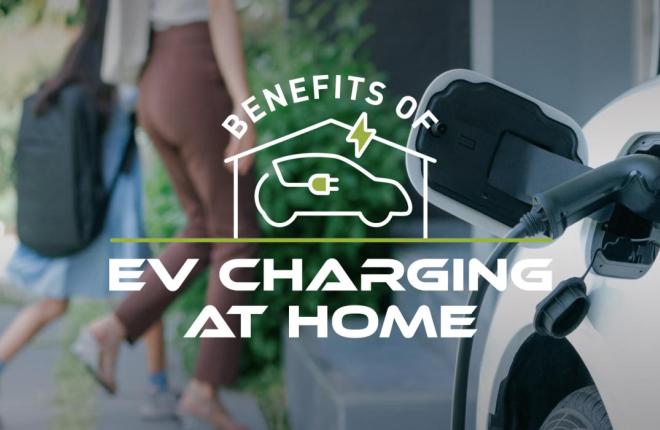
The Benefits of Having Your Own EV Charger at Home
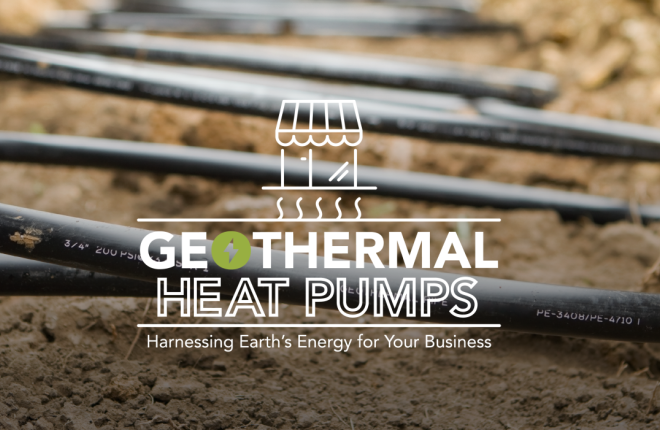
Geothermal Heat Pumps: Harnessing Earth's Energy for Your Business
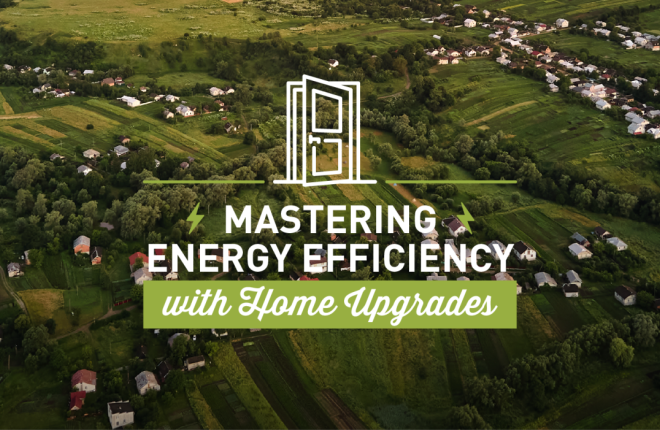
Mastering Energy Efficiency with These Home Upgrades
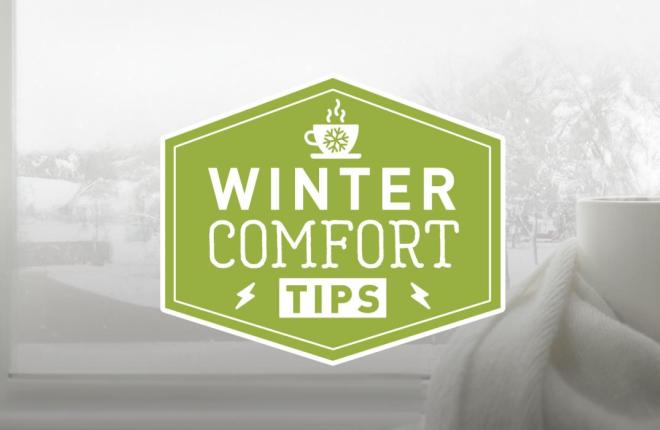